Нео Фициал. «Как клепали корабли и небоскрёбы»
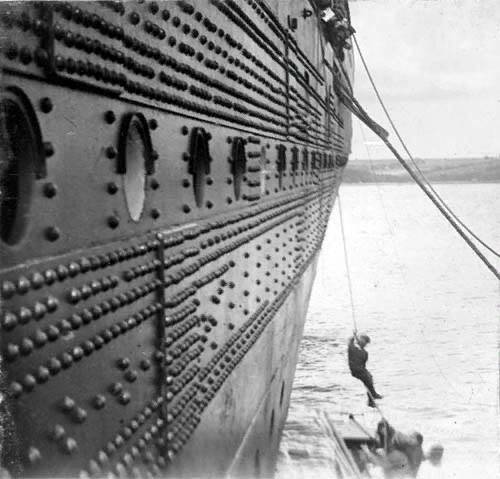
Представьте себе мир без сварки. Уже строятся металлические корабли, котлы, цистерны… Да много чего металлического. А сварки не существует. Как скрепляли друг с другом металлические листы? Склёпывали. А теперь представьте, какой это был геморрой (или головная боль — кому что ближе).
Сначала нужно насверлить или пробить отверстия в листах металла (для этого и пробойник специальный изобрели). Причём так, чтобы они микрон в микрон совпадали друг с другом. Ведь заклёпка должна полностью заполнить отверстие. Уже задачка, да? Эта задача решалась тоже весьма хлопотным путём — сначала пробивались отверстия меньшего, чем необходимо, диаметра, потом листы стягивались болтами и отверстия высверливались до нужного диаметра. Каждое.
Потом в эти отверстия нужно забить заклёпки. Сначала специальный человек в специальной жаровне греет их до нужной температуры (нельзя ни перегреть, ни недогреть). Потом заклёпку быстро-быстро пока не остыла толкают в отверстие и расклёпывают. КАЖДУЮ! Дорого, долго, трудно. Примерно так:
Таким образом склепали, например, Титаник. Больше трёх миллионов заклёпок потратили. Как вам цифирка? Вот так его строили:
И вот, что получилось:
Вообще-то соединение с помощью заклёпок было известно очень давно, но расцвело, когда металл стал основным конструкционным материалом. И клепали всё, что из него изготовлялось. Вот пара моих снимков. Цистерна из ростовского железнодорожного музея:
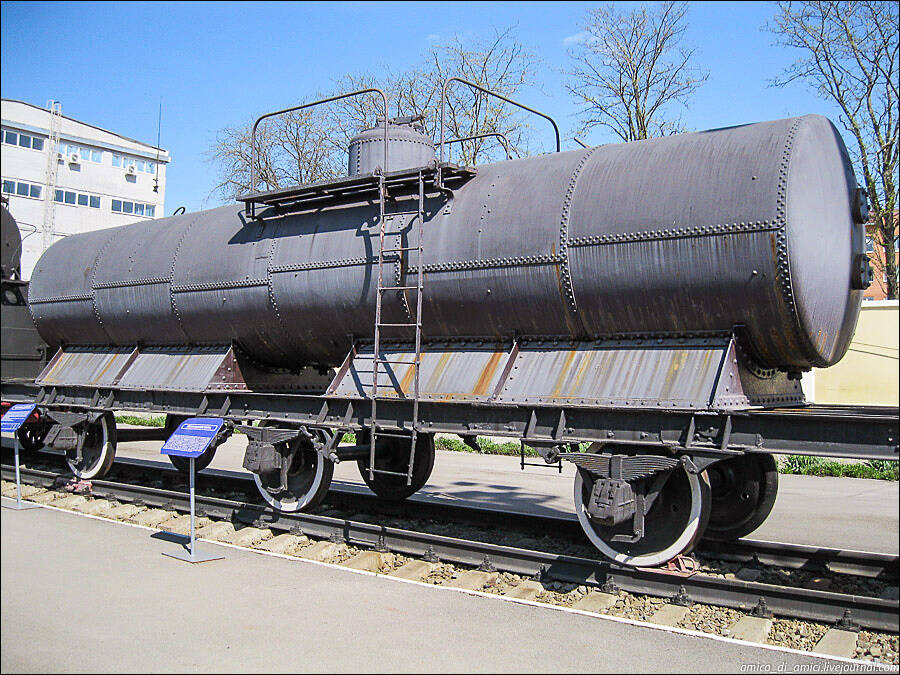
Цистерна из ростовского железнодорожного музея
Кстати, обратите внимание, сколько у неё осей. А эту бочку откопали при земляных работах в Севастополе. Я думать не думал, что было время, когда металлические бочки тоже клепали:
Но давайте вернёмся к морю. Когда паровые машины уверенно шагнули на борт кораблей, стало ясно, что дерево как материал уже не подходит. Постоянная вибрация машин расшатывала конструкцию корпуса и пытаясь её упрочить дошли до того, что чуть не половину водоизмещения стал составлять его собственный вес.
После изобретения прокатного стана препятствий к постройке кораблей из железных листов не стало. И, кстати, вес металлических корпусов составлял лишь 30-35% водоизмещения. А опыт сшивания металла заклёпками уже был, те же паровые котлы тоже клепали, ещё из кованых листов. И дело пошло, как я уже говорил, только на один «Титаник» больше трёх миллионов заклёпок потратили.
Первый вопрос — а как сделать отверстия под клёпки? Электрических или пневматических сверлильных устройств ещё не было. А их попросту пробивали! В 1805 году английский изобретатель и промышленник Модсли запатентовал дыропробивную паровую машину. Основной проблемой стало пробить эти дыры в листах металла всевозможной формы, чтобы они точно совпадали. В цеху по чертежам с помощью тщательной разметки пробивали отверстия, но несколько меньшего диаметра. Потом на месте сборки листы точно совмещали, фиксировали болтами и с помощью специального инструмента прогоняли отверстия до нужного диаметра, устраняя при этом их несоосности.
Ладно, пробивали горячие листы, допустим. Но расширяли до нужного диаметра холодные. И я так понимаю, корабельная сталь на обшивку была толщиной несколько сантиметров, а не миллиметров. Интересно было бы посмотреть на этот инструмент… Вероятно отверстия все же рассверливали, а затем проходили разверткой для точности.
Теперь сама заклёпка. Она должна быть из того же материала, что и листы, чтобы не получалось гальванических пар, особенно это опасно в морской воде. Заклёпка должна не только скрепить детали, но и заполнить собой всё отверстие, в которое она вставлена. Для этого её нагревают в среднем до 1000 градусов. С той стороны, где уже есть головка, её поддерживают каким -нибудь массивным упором, а с другой стороны лупят молотом. Но не по самой заклёпке, а по так называемой обжимке, которую держит второй рабочий. Обычно это металлический цилиндр, в одном торце которого есть полусферическое углубление, которое сформирует вторую головку. Делать это надо очень быстро, чтобы заклёпка не успела остыть ниже 600-500 градусов. Греют их в специальных переносных коксовых печах обычно подростки:
А дело это ответственное. Перегреешь — при остывании заклёпку может попросту порвать. Недогреешь — на завершающей стадии расклёпывания температура может упасть ниже установленного предела, сталь станет синей и ломкой, могут появиться трещины. Клёпаные швы могут быть прочными, это обычно несущие конструкции, где не требуется герметичность. А могут быть плотными, где особенно важна герметичность, вот как раз корабельные корпуса. И могут быть прочноплотными, ну, вы поняли.
Плотные швы предварительно накрепко стягивались болтами. Заклёпка по ходу процесса должна полностью заполнить собой отверстие и обе головки плотнейшим образом прилегать к поверхности. И потом ещё может производиться дополнительная уплотняющая операция:
Так называемая чеканка шва. Кроме того, между листами по шву прокладывались ленты из прочной ткани, пропитанные водоотталкивающим веществом. Всё это давало желаемый результат, что подтверждает герметичность клёпаных корпусов подводных лодок во время Второй мировой войны, а уж что над ними не вытворяли — и бомбили, и ныряли на 200 с лишним метров.
А в заключение ещё два снимка. Вот мальчишки разогревают заклёпки. Возможно, они носятся по уложенным доскам, передавая клепальщикам разогретые заклёпки.
Но есть и другой способ.
Вот снимок со строительства небоскрёба, с судоверфи не нашёл. Замучаешься таскать печь с место на место по балкам и этажам, или бегать по ним с заклёпкой, проще перекинуть её. Пишут, что кидали до 30 метров.
Тут уже видно, что клёпка ведётся с помощью пневмоинструмента. Но нам интересен правый рабочий. Что за ведро у него в руке? А вот он им как раз и ловил летящие раскалённые заклёпки, хватал клещами в другой руке и вставлял в отверстие. Скорее всего и на судоверфях так делали, когда корпус вырастал в высоту.
Исчезла ли клёпка сейчас? Отнюдь. Есть ряд конструкций, где сварка заменить её не может. А уж что касается авиации, то и говорить нечего.
Leave a reply
Для отправки комментария вам необходимо авторизоваться.